The making
All my pieces are made on a potter's wheel and shaped by hand. I don’t use rulers or molds.
You can find pieces that match, but you won’t find two that are the same.
I take a lot of time to create a piece and work with passion and attention to detail.
After a day, the piece is leather-hard and can be trimmed. This is the moment the pot gets its final shape. Sometimes I like to give the pot some structure so the glazes will break and flow, sometimes I want the clay to be as smooth as sea glass or beach pebbles, then they have to be polished.
The bisque firing
When the pot is completely dry, it gets fired to 1040ºC. During this firing, the clay gets stronger and loses gases, but it is still porous enough to absorb the glazes.
The glazing
I glaze all my pots with a brush so I can create an interesting surface, with a lot of colour variation. I love the create mini landscapes. The way the glazes look before and after firing differs a lot. The colors aren’t always the same, so can a glaze that’s red before firing, turn blue during firing. It takes a lot of testing to learn how the glazes react to the heat and to each other.
I work with a beautiful clay body that affects the outcome of the glazes in a positive way. I glaze the outside just partly so the clay can be seen and felt. I only use commercially made non-toxic, lead free and food safe glazes. It’s dishwasher safe, no hand washing is necessary.
The glaze firing
When the glaze is completely dry, the pot gets fired for the second time. This time, at 1220ºC, it becomes vitrified and waterproof. I use green energy to fire my kilns.
The kiln can be opened when the pieces are around 60ºC.
That's the moment I see if they came out as I wanted, and if they're ready to start their journey to you.
.
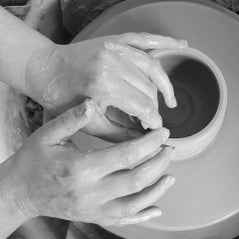